Single screw extruder machines are widely used in the plastic and food industries for processing materials. These machines consist of a single rotating screw that pushes material through a heated barrel. The design of single screw extruders allows for continuous processing, making them efficient for various applications. Understanding energy efficiency in these machines is crucial for reducing operational costs and minimizing environmental impact.
Importance of Energy Efficiency
Energy efficiency is a critical factor in the operation of single screw plastic extruder machines. High energy consumption can lead to increased operational costs and a larger carbon footprint. By improving energy efficiency, manufacturers can reduce their energy bills and contribute to sustainability efforts. This not only benefits the environment but also enhances the overall profitability of the production process.

Factors Affecting Energy Efficiency
Several factors influence the energy efficiency of single screw extruder machines. These include the design of the screw, the type of material being processed, and the operating conditions. A well-designed screw can optimize material flow and reduce energy consumption. Additionally, the properties of the material, such as viscosity and temperature, can significantly impact energy usage during processing.
Optimizing Screw Design
Optimizing the screw design is one of the most effective ways to enhance energy efficiency in single screw extruder machines. The geometry of the screw, including its diameter, length, and flight depth, plays a vital role in material transport and mixing. Engineers can design screws that minimize energy loss by ensuring efficient material flow and reducing friction within the barrel.
Material Selection
The choice of material being processed also affects energy efficiency. Different materials have varying thermal and mechanical properties, which can influence the energy required for processing. Selecting materials that are easier to process can lead to lower energy consumption. Additionally, using additives that improve flow characteristics can enhance the overall efficiency of the extrusion process.
Temperature Control
Maintaining optimal temperature control is essential for energy efficiency in single screw extruder machines. The heating elements in the barrel must be carefully regulated to ensure that the material reaches the desired processing temperature without excessive energy use. Implementing advanced temperature control systems can help maintain consistent temperatures, reducing energy waste and improving product quality.
Variable Speed Drives
Incorporating variable speed drives (VSDs) in single screw extruder machines can significantly improve energy efficiency. VSDs allow for precise control of the screw speed, enabling operators to adjust the processing parameters based on the material being extruded. By optimizing the screw speed, manufacturers can reduce energy consumption while maintaining product quality.
Regular Maintenance
Regular maintenance of single screw extruder machines is crucial for ensuring energy efficiency. Over time, wear and tear can lead to decreased performance and increased energy consumption. Implementing a routine maintenance schedule can help identify and address issues before they escalate, ensuring that the machine operates at peak efficiency.
Monitoring Energy Consumption
Monitoring energy consumption is essential for identifying areas for improvement in energy efficiency. By tracking energy usage over time, manufacturers can pinpoint inefficiencies and implement corrective measures. Utilizing energy monitoring systems can provide valuable insights into the performance of single screw extruder machines and help optimize their operation.
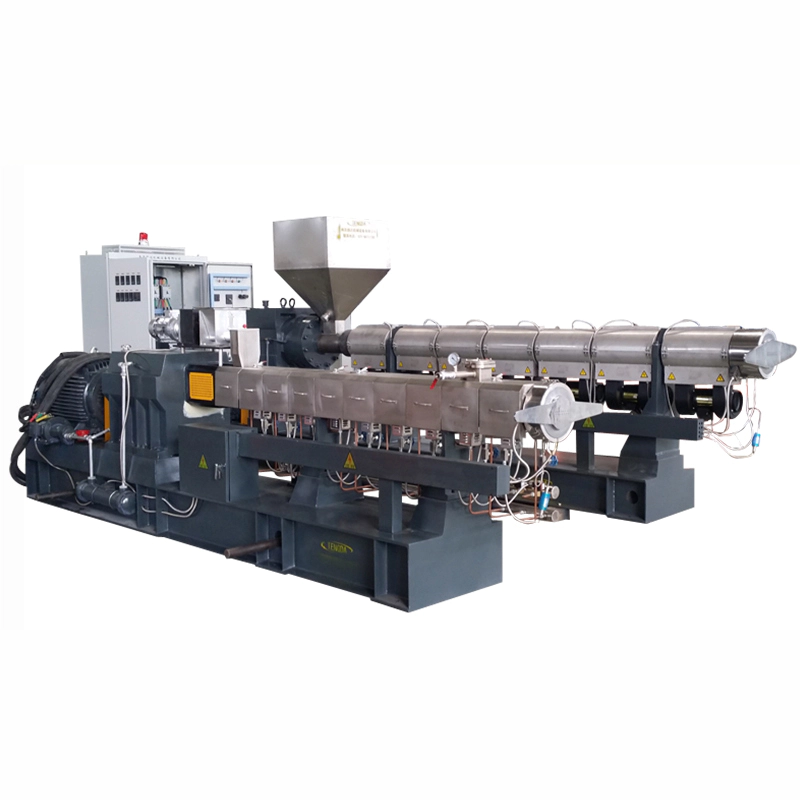
Training Operators
Training operators on best practices for operating single screw extruder machines can also contribute to energy efficiency. Well-trained operators are more likely to recognize and address issues that may lead to increased energy consumption. Providing ongoing training and resources can empower operators to make informed decisions that enhance the efficiency of the extrusion process.
Conclusion
In conclusion, energy efficiency in single screw extruder machines is a multifaceted issue that requires attention to various factors. By optimizing screw design, selecting appropriate materials, maintaining temperature control, and implementing advanced technologies, manufacturers can significantly improve energy efficiency. Regular maintenance and operator training further enhance these efforts, leading to reduced operational costs and a smaller environmental footprint. As industries continue to prioritize sustainability, focusing on energy efficiency in single screw extruder machines will be essential for future success